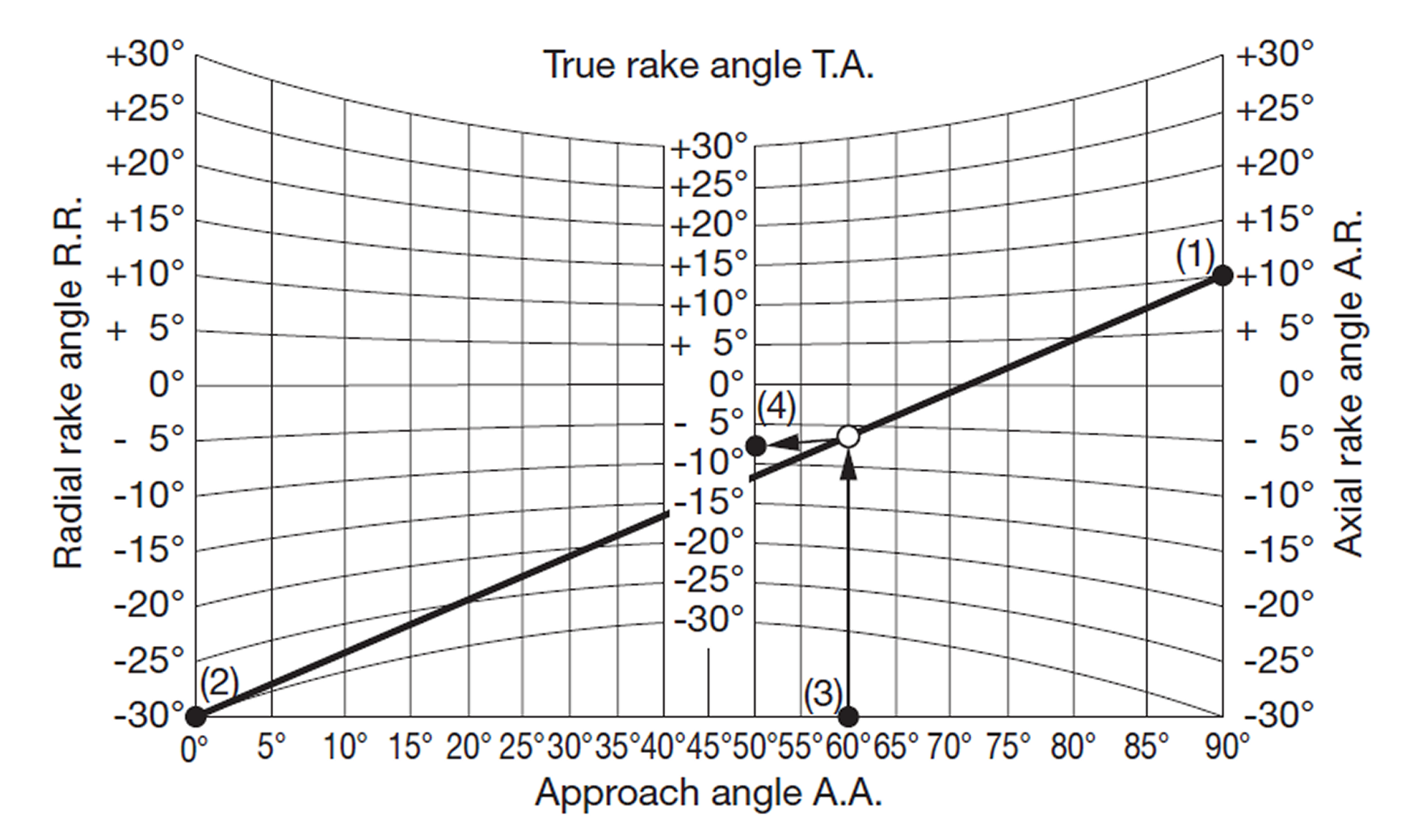
# | Symbol | Material | Function | Effect |
---|---|---|---|---|
1 | AR | Axial rake angle | Determines chip evacuation direction, adhesion, thrust, etc. | Available in positive to negative (large to small) rake angles. Typical combinations: Positive and Negative, Positive |
2 | RR | Radial rake angle | Determines chip thickness and chip evacuation direction | Large: Thin chips, small cutting force |
3 | AA | Approach angle | Effective rake angle | Positive (Large): Excellent machinability and low chip adhesion. Low cutting edge strength. Negative (Small): Strong cutting edge and easy chip adhesion |
4 | TA | True rake angle | Determines chip control direction | Positive (Large): Excellent chip control and small cutting force. Low cutting edge strength |
5 | IA | Cutting edge inclination angle | Determines surface finish roughness | Small: Excellent surface roughness |
6 | FA | Face cutting h angle | Determines cutting edge strength, tool life, chattering | — |
# | Symbol | Material | Function | Effect |
---|---|---|---|---|
1 | AR | Axial rake angle | Determines chip evacuation direction, adhesion, thrust, etc. | Available in positive to negative (large to small) rake angles. Typical combinations: Positive and Negative, Positive |
2 | RR | Radial rake angle | Determines chip thickness and chip evacuation direction | Large: Thin chips, small cutting force |
3 | AA | Approach angle | Effective rake angle | Positive (Large): Excellent machinability and low chip adhesion. Low cutting edge strength. Negative (Small): Strong cutting edge and easy chip adhesion |
4 | TA | True rake angle | Determines chip control direction | Positive (Large): Excellent chip control and small cutting force. Low cutting edge strength |
5 | IA | Cutting edge inclination angle | Determines surface finish roughness | Small: Excellent surface roughness |
6 | FA | Face cutting h angle | Determines cutting edge strength, tool life, chattering | — |
# | Failure | Basic Remedies | Countermeasures (Example) | ||||||||||||
---|---|---|---|---|---|---|---|---|---|---|---|---|---|---|---|
Cutting Edge Failure | |||||||||||||||
1 | Failure 1 | Sharpen blade regularly |
|
||||||||||||
2 | Failure 2 | Reduce feed rate |
|
||||||||||||
3 | Failure 3 | Change tool material |
|
||||||||||||
4 | Failure 4 | Check spindle runout |
|
||||||||||||
Others | |||||||||||||||
1 | Failure 1 | Clean work area |
|
||||||||||||
2 | Failure 2 | Train operators |
|
||||||||||||
3 | Failure 3 | Regular maintenance |
|
||||||||||||
4 | Failure 4 | Replace worn components |
|